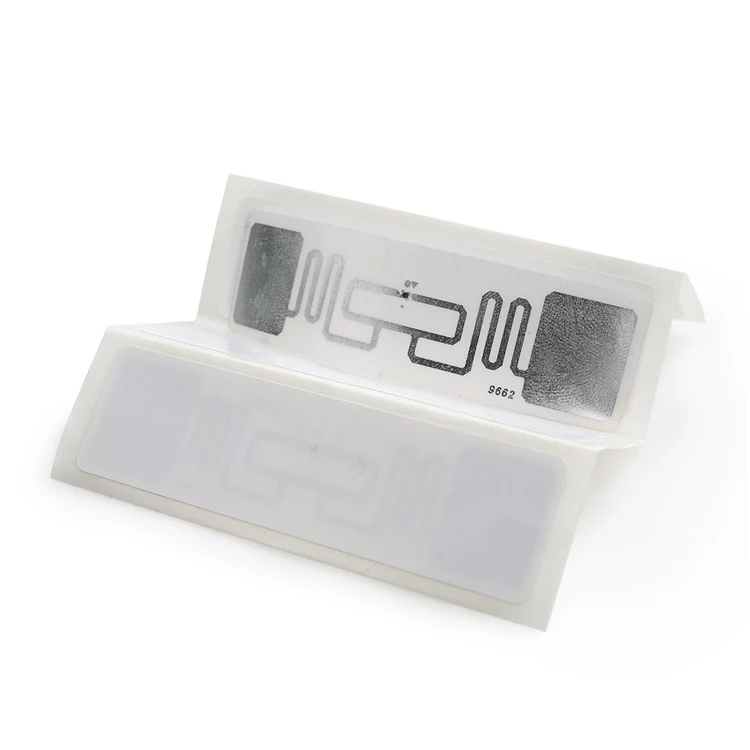
UHF RFID Label: Revolutionizing Warehouse Management in Logistics
Discover how UHF RFID labels streamline logistics and inventory management, enhancing efficiency, accuracy, and sustainability in your operations.
Efficient management of uniforms and linens is crucial for various industries, including hospitality, healthcare, and manufacturing. RFID (Radio Frequency Identification) technology has emerged as a game-changer in this sphere, providing reliable tracking solutions that streamline operations, reduce losses, and enhance inventory management. This article delves into the benefits and applications of RFID chips for uniforms and linens, offering insights into how this technology can transform laundry management. If you’re looking to improve your operational efficiency and reduce costs, this article is worth your time.
RFID chips are small electronic devices that use radio waves to communicate information. They consist of a chip and an antenna, allowing them to transmit data to RFID readers. When an RFID tag comes within range of a reader, it sends its stored information, such as a unique identification number, which can then be used for tracking and management purposes.
In the context of uniforms and linens, RFID technology provides a seamless way to monitor and manage items throughout their lifecycle. By embedding RFID chips into textiles, organizations can automate the tracking process, leading to improved efficiency and reduced manual errors.
The use of RFID for tracking uniforms and linens offers numerous advantages. Firstly, it significantly reduces the time and labor involved in inventory management. Traditional methods, such as barcode scanning, require line-of-sight and manual input, which can be time-consuming and prone to errors. RFID, on the other hand, allows for simultaneous scanning of multiple items, enhancing operational efficiency.
Moreover, RFID technology provides real-time data on inventory levels, enabling organizations to make informed decisions about stock management. This capability is particularly beneficial in industries where timely access to uniforms and linens is critical, such as in hospitals and hotels.
RFID chips play a pivotal role in laundry management by automating the tracking of items through various laundry processes. From the moment a uniform or linen is collected to its return after laundering, RFID technology ensures accurate tracking at every stage.
For instance, RFID readers installed at various points in the laundry process can quickly identify and log items as they move through washing, drying, and folding. This automation reduces the likelihood of lost or misplaced items, leading to improved accountability and customer satisfaction.
When selecting RFID chips for laundry applications, it’s essential to consider key features that enhance their functionality. Some of these features include:
Durability: RFID chips designed for laundry must withstand harsh conditions, including high temperatures, moisture, and chemical exposure. For instance, the RFID chips specified in this article can endure washing temperatures of up to 90°C and sterilization temperatures of 135°C.
Water and Chemical Resistance: Effective RFID chips are water-resistant and can withstand various detergents, softeners, and bleach, ensuring their longevity even after repeated laundering.
Memory Capacity: RFID chips typically come with different memory capacities. The chips discussed here feature 128 bits of EPC memory and 512 bits of user memory, allowing for the storage of essential data relevant to each item.
Choosing the right RFID chip for your uniforms and linens involves assessing several factors, including:
Application Environment: Consider the conditions in which the RFID chips will be used. For example, if the items undergo frequent washing and exposure to chemicals, opt for durable and resistant tags.
Read Range Requirements: Depending on your operational needs, you may require RFID chips with different read ranges. Ensure that the chips you select can be read effectively in your specific environment.
Integration with Existing Systems: It’s crucial to choose RFID chips that can seamlessly integrate with your current inventory management systems to maximize efficiency.
Various industries can significantly benefit from RFID tracking solutions, particularly those that manage large inventories or have intensive laundering needs:
Healthcare: Hospitals use RFID to track medical uniforms and linens, improving compliance, reducing loss, and ensuring hygiene. It also helps manage equipment like surgical tools.
Hospitality: Hotels benefit from RFID for tracking linens, towels, and uniforms, helping prevent loss and maintaining consistent inventory levels for exceptional guest experiences.
Manufacturing: In industrial settings, RFID is used to manage uniforms and protective gear, ensuring workers are compliant and inventory is organized.
Retail: Retailers can use RFID to track merchandise effectively, reducing theft and improving inventory accuracy. This technology supports better stock management for uniforms or work apparel as well.
Laundry Services: Dedicated laundry facilities leverage RFID to streamline the processing of garments and linens, increasing throughput and accuracy while minimizing manual errors.
RFID chips enhance inventory control through several key mechanisms:
Real-Time Tracking: RFID provides real-time visibility into inventory levels, allowing organizations to monitor stock efficiently and reduce the risk of overstocking or stockouts.
Automated Data Capture: Unlike barcodes that require manual scanning, RFID allows for the automatic collection of data as items pass through checkpoints. This speeds up inventory processes and reduces human error.
Improved Accuracy: With RFID tracking, organizations can achieve higher accuracy in inventory counts, minimizing discrepancies that often arise with manual counts and traditional methods.
Enhanced Reporting and Analytics: RFID systems can generate detailed reports on inventory movement, usage patterns, and turnover rates, enabling organizations to make informed decisions based on data analytics.
While RFID has many benefits, there are challenges associated with its implementation in laundry operations:
Initial Costs: The upfront investment in RFID technology, including tags, readers, and software systems, can be significant. Organizations need to balance initial costs with long-term savings.
Integration with Existing Systems: Integrating RFID technology into current operations and management systems can be complex, requiring thorough planning and possibly new software solutions.
Tag Durability: Ensuring that RFID tags can withstand harsh laundry processes, including high temperatures and chemical exposure, is crucial. The selection of tags must be appropriate for the specific laundering conditions.
Staff Training: Employees need proper training to utilize RFID systems effectively. This includes understanding how to handle RFID equipment and interpret data for optimized management.
Interference Issues: RFID systems can face interference from metals or water, which can affect read accuracy. Selecting the right technology and placement of readers can mitigate such challenges.
Integrating RFID technology into existing systems involves a strategic approach:
Assess Current Processes: Evaluate current inventory and laundry management practices to identify areas where RFID can provide improvements.
Choose the Right Technology: Determine the specifications needed for tags and readers based on your environment (e.g., UHF vs. HF RFID) and the types of textiles being managed.
Develop a Clear Integration Plan: Create a detailed plan that outlines how RFID will be integrated into existing operations. This should include timelines and roles for staff.
Invest in Necessary Infrastructure: Ensure your facilities have the right infrastructure, such as RFID readers placed at key locations throughout laundry operations (e.g., collection areas, washing, drying, and folding zones).
Pilot Program: Start with a pilot program to test RFID in a small, controlled environment. This allows for adjustments before a full rollout.
Train Staff: Provide comprehensive training for staff on how to use RFID technology and understand the data generated to enhance operational efficiency.
Monitor and Adjust: After full implementation, continuously monitor the system’s performance and be open to making adjustments based on feedback and observed challenges.
By addressing these critical areas, organizations can successfully integrate RFID technology and leverage it to enhance their laundry management and inventory control processes.
Newest trends and common knowledge in RFID laundry tags.
Discover how UHF RFID labels streamline logistics and inventory management, enhancing efficiency, accuracy, and sustainability in your operations.
RFID tag technology enhances food and beverage processing by improving efficiency, safety, and management effectiveness, revolutionizing traditional practices.
Discover the NXP ICODE SLIX RFID inlay: efficient, versatile, and engineered for secure product tracking and authentication across various industries.
Didn’t find what you want? Ask our manager for help!