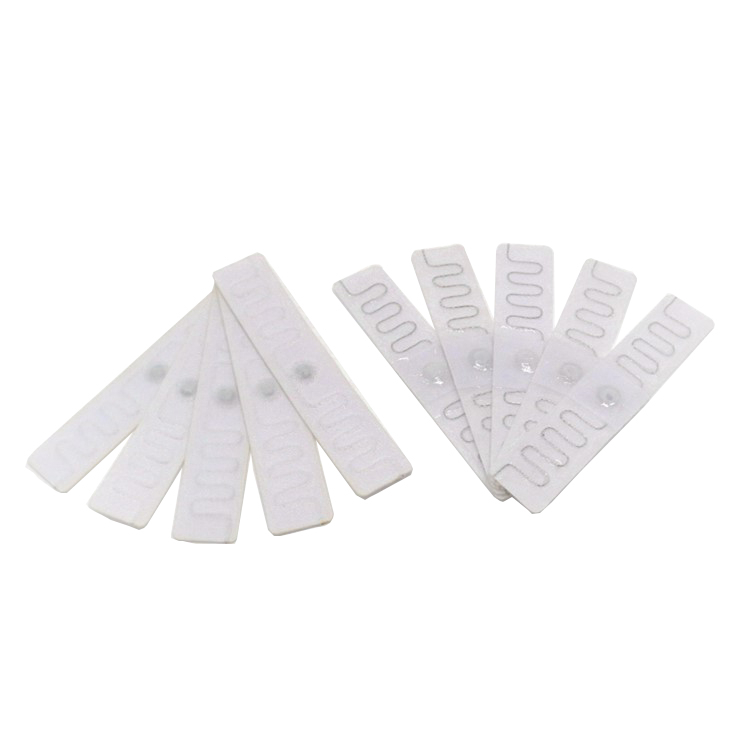
RFID Tag for Industrial Laundry
RFID Tag for Industrial Laundry,it’s RFID linen chips automate textile tracking in industrial laundry, enhancing inventory accuracy, reducing labor costs, and improving asset management.
With the rapid development of modern industry and ongoing technological advancements, the safe operation and maintenance of equipment have become increasingly important. Enterprises need to ensure that their equipment operates efficiently while minimizing failures and downtime, thereby improving productivity and economic benefits. Equipment inspection, as a critical aspect of maintenance management, plays a vital role in identifying potential issues in a timely manner, allowing for effective measures to be implemented. The introduction of RFID technology greatly facilitates the intelligent and efficient management of equipment inspections.
RFID (Radio Frequency Identification) technology is a non-contact automatic identification technology that uses radio frequency signals. By integrating RFID tags with RFID handheld terminals, such as PDAs, quick recognition and data acquisition of objects are made possible. An RFID system generally consists of three main components: RFID tags, RFID handheld terminals or readers, and a database. RFID Tags can be attached to various pieces of equipment to store relevant information, while readers are responsible for reading the data from the tags and transmitting it to the database system for processing and analysis.
Automation of Inspection Processes
Traditional equipment inspections typically rely on manual checks, which can be influenced by subjective factors, leading to inaccuracies and omissions in data collection. The integration of RFID technology enables the automation of the inspection process. Inspection personnel only need to carry an RFID handheld terminal or PDA; by scanning the RFID tags on the equipment along the designated inspection path, they can quickly retrieve basic information, current usage status, and historical maintenance records of the equipment. This automation significantly reduces the time required for manual operations and enhances inspection efficiency.
Real-time Data Collection
RFID tags make the data collection during equipment inspections more immediate and accurate. During inspections, RFID handheld terminals can not only read the equipment status but also upload data in real time to a central database. This provides equipment management personnel with a platform for real-time monitoring, enabling them to keep track of the equipment’s operating conditions at all times, promptly identify any anomalies, and swiftly take necessary action. Consequently, the efficiency of equipment maintenance and management is notably improved.
Enhanced Data Accuracy
The human factor often results in errors and omissions in traditional inspection methods. In contrast, RFID technology eliminates potential errors during manual data recording by automating the identification process, thus ensuring data accuracy and completeness. Records of maintenance work can be directly stored in a database, allowing for automatic generation of maintenance reports, thereby reducing data inaccuracies caused by human involvement and increasing the reliability of the information.
Improved Traceability of Equipment Management
In large enterprises where equipment diversity and wide distribution present significant management challenges, effective oversight of equipment becomes complex. The application of RFID technology allows each piece of equipment to be uniquely identified and tracked. By recording the date, time, personnel involved in each inspection, and the historical failures of the equipment, managers can gain clear insights into the equipment’s usage and maintenance history. This traceability provides a reliable basis for subsequent equipment repairs and management decisions.
Reduction of Maintenance Costs
By optimizing the inspection processes, RFID inspection tags not only enhance inspection efficiency but also significantly reduce maintenance costs. By minimizing human intervention and improving data accuracy, company resources can be utilized more effectively. Moreover, real-time data analysis and notifications of anomalies can effectively prevent equipment failures, thereby reducing losses caused by unexpected downtime. This systematic and proactive management approach aids enterprises in achieving higher economic benefits.
The integration of RFID tag in equipment inspection management revolutionizes traditional methods, leading to a paradigm shift toward more efficient, accurate, and cost-effective operations. By automating processes, providing real-time data, and ensuring traceability, RFID aids enterprises in not only enhancing productivity but also optimizing resource utilization. As industries continue to evolve, the role of innovations like RFID in maintenance management will be crucial for sustaining operational excellence and driving economic success.
Newest trends and common knowledge in RFID laundry tags.
RFID Tag for Industrial Laundry,it’s RFID linen chips automate textile tracking in industrial laundry, enhancing inventory accuracy, reducing labor costs, and improving asset management.
Efficient laundry management is crucial for businesses in various sectors, including hospitality, healthcare, and industrial laundry services. RFID laundry tags have emerged as a game-changer, offering enhanced tracking, inventory management, and operational efficiency.
RFID tags (Radio Frequency Identification tags) are electronic labels that use radio waves for data transmission and storage.
Didn’t find what you want? Ask our manager for help!